What is a Globe Control Valve?
A globe control valve is a type of valve that regulates the flow of liquids, gases, or steam within a pipeline. It has a globe-shaped body and is designed to provide precise control over flow rates and is often used for throttling, meaning it can adjust the flow to maintain specific conditions like pressure, temperature, or flow rate.
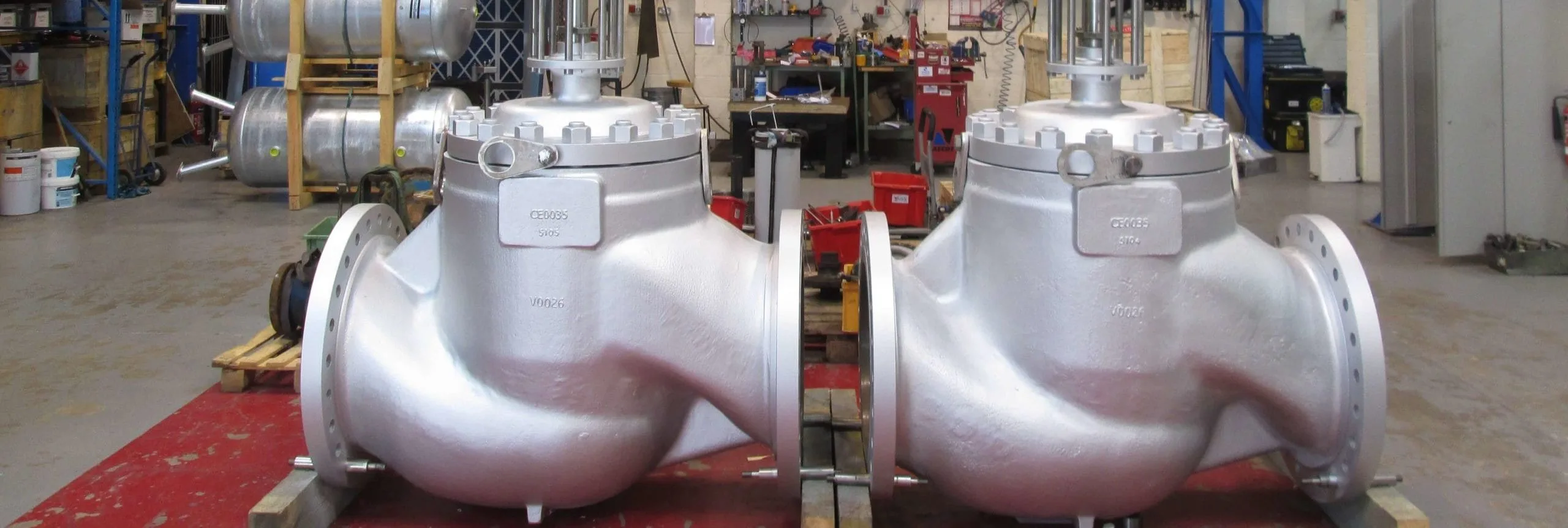
In What Industries Are Globe Control Valves Commonly Used?
Globe control valves are essential in industries which require precise control over the fluid flow, under varying pressure and temperature conditions. Most typically, globe control valves are used in industries such as chemical processing, oil and gas, power generation, water treatment, HVAC, and pharmaceutical manufacturing.
What Are the Benefits of Using a Globe Control Valve?
Globe control valves have many benefits, making them a popular choice for precise flow regulation in various industries.
- Precise Flow Control: Globe control valves offer excellent throttling capabilities, which allow for precise regulation of flow rates. This makes them an ideal choice for applications that require accurate control over liquid or gas flow.
- Good Performance at High Pressure: Designed with an efficient flow path and tight sealing capabilities, globe control valves are designed to deliver optimal performance and remain stable in high-pressure applications.
- Versatile: Due to their ability to control flow in both low and high-pressure systems, globe control valves can be used in a wide range of applications, including water, steam, gas, and chemical.
- Adjustable Actuation: Globe valves can be equipped with manual or automated actuators, offering flexibility for both manual operation and automated systems in industries like oil & gas, chemical, and power generation.
- Improved Flow: Globe control valves have a streamlined internal structure and flow path designed to minimise pressure loss while maintaining flow control, improving system efficiency and ensuring a more controlled movement of fluid.
- Durability: This type of valve is designed to be highly durable and resistant to wear and corrosion, as they are made from strong materials like Carbon Steel, stainless steel or more exotic materials such as Suplex and Super Duplex to ensure long service life.
- Easy Maintenance: The simple, modular construction of globe control valves allows for a straightforward disassembly and reassembly, for easy and accessible maintenance. Internal components, such as the stem, plug, and seat, are easily accessible for easy maintenance and replacement, reducing the downtime in industrial operations. For more information about maintenance services go to our Control Valve Maintenance and Repair page.
What Are the Components of a Globe Control Valve?
Globe control valves are made up of several complex components that all work together to regulate the flow of fluids within a system. These elements include the valve body, the seat, plug, stem, bonnet, packing, actuator and flow control trim – and all play an important function in operating the control valve.
- Valve Body: The valve body is the main housing that contains all the internal parts of the globe control valve. The casing is designed to withstand high pressures and temperatures while directing the flow of fluids through the valve.
- Seat: The seat is the surface that the valve plug rests against to control fluid flow. Designed to prevent leakage, the seat forms a tight seal when the valve is closed, preventing leakage.
- Plug: The plug is the key moving component that controls the flow in the control valve by adjusting the size of the opening between the seat and the plug. The position that the plug is in will determine the flow rate, either restricting or allowing the passage of fluid.
- Stem: The stem connects the plug to the actuator, controlling the plug’s position, either opening or closing it to regulate the fluid flow.
- Bonnet: The bonnet is the protective cover that encloses the stem, packing, and mounting for the actuator. It serves as a barrier to secure internal moving components.
- Packing: The packing in a globe control valve is the material used to seal the valve stem, preventing leaks between the stem and the bonnet. The packing requires routine maintenance to ensure it remains effective in preventing fluid leakage.
- Actuator: This mechanical, pneumatic, Electric or Hydraulic device provides the force to move the stem and plug, adjusting the valve’s position to control the valve’s flow regulation. It can be operated manually or automated through electric, pneumatic, or hydraulic mechanisms, depending on the application.
- Flow Control Trim: The flow control trim is a combination of the Valve plug, seat and Cage, the design enhances the valve’s ability to precisely regulate fluid flow depending on the trim characteristic selected, the most common being Equal Percent, Linear or Quick opening. This is because the trim can influence the pressure drop across the valve, and adjust the size of the flow area through the valve.
What Are the Different Globe Control Valve Body Designs?
There are several globe control valve designs, each tailored to meet specific needs and perform effectively in different environments and applications.
Straight-Pattern Globe Valve
The straight-pattern globe valve, also referred to as the 2-way globe valve, design ensures the flow passes directly through the valve body in a linear configuration i.e. the valve inlet and outlet are inline. In this valve design, the trim can be engineered to either minimise or maximise flow resistance. This type of valve design is ideal for a multitude of applications such as high-pressure low-flow or low-pressure high-flow applications and tends to be the most common control valve type.
Angle Globe Valve
Angle globe valves have a 90-degree turn in the flow path, designed to allow the fluid to change direction between the inlet and outlet. This valve design helps save space and can accommodate specific piping layouts where a change in direction is needed. An angle globe valve is suited for pipelines where space constraints make a straight-through valve impractical.
Three-Way Globe Valve
A three-way globe valve is designed with three ports, including one inlet and two outlets, or vice versa. This type of valve is typically used for mixing or diverting fluids, and can either mix two flow streams or split one flow into two different directions. This valve design is best for applications where precise fluid control is crucial, such as chemical processing, water treatment systems, or HVAC systems (for temperature control).
What Are the Different Trim Designs?
There are various globe valve trim designs that are best suited to different applications and their specific operational needs:
Standard Trim
The standard trim design consists of a basic plug, seat, and stem design that provides reliable and efficient flow control for general purposes. It’s simple and versatile, but not specialised trim is commonly used in systems that don’t require extreme precision, like water supply systems and HVAC applications.
Pressure-Reducing Trim
The pressure-reducing trim has features designed to reduce and regulate pressure within a system. This trim is perfect for applications that need to control high incoming pressures and reduce them to a more manageable level. This could be used in steam lines, water distribution, high-pressure chemical feed systems as well as numerous oil and gas applications.
Balanced Trim
A balanced trim design uses a pressure-balanced plug to counteract the forces acting on the valve plug. This trim is ideal for systems where the out-of-balanced forces on the plug would normally be high due to a greater pressure differential in the valve. This allows the actuator to maintain better authority over the process and reduces the need for oversized actuators. Typically this type of trim is utilised where the pressure differential is high, like oil or gas pipelines, as it can ensure the valve can maintain stable control over the flow.
Cage-Trim
The cage-trim design has a cage surrounding the valve plug. The cage’s purpose is to control the flow path and reduce the potential for cavitation or noise within the valve, making it suitable for high-flow and high-pressure conditions. Cage-trim designs are often used in high-pressure drop applications for various flow conditions.
Bellow-Sealed Trim
The bellows seal prevents leakage of fluids around the valve stem by providing a tight seal, even in challenging conditions. Bellow-sealed trims are great for applications involving toxic, corrosive, or hazardous fluids, as they ensure no leakage into the environment.
Teflon-Seated Trim
Teflon-seated trims or soft-seated trims use a seal that is made from Polytetrafluoroethylene (PTFE), suited for applications that require a tight shut off.
Metal-Seated Trim
A metal-seated trim is made from durable metal that can withstand extreme temperatures and pressures, providing long-lasting performance in harsh conditions. This trim is typically used in applications in oil refineries, high-temperature steam systems, and high-pressure gas pipelines.
Low-Flow Trim
Low-flow trim designs feature a small, fine-tuned seat and plug combination, which allows for very controlled, low-flow regulation. This type of trim is best for globe control valves where small amounts of fluid need to be regulated with high precision – perfect for use in laboratory fluid control or chemical dosing systems.
Anti-Cavitation Trim
Anti-cavitation trims have special features that reduce the pressure in stages and feature a low recovery factor designed to prevent cavitation such as a multi-hole caged trim. Trim designs like this are essential for systems where pressure drops can cause cavitation and lead to damage to the valve, like in high-pressure water or steam systems.
Multi-Stage Disc Stack
This trim features a multi-stage disc stack designed to help significantly reduce pressure in severe service applications. The multiple stages gradually reduce pressure, reducing the risk of damage from sudden pressure fluctuations. Multi-stage disc stack trims are typically used in pump testing, water injection valves on offshore rigs, gas pipelines, and other high-pressure, severe service environments.
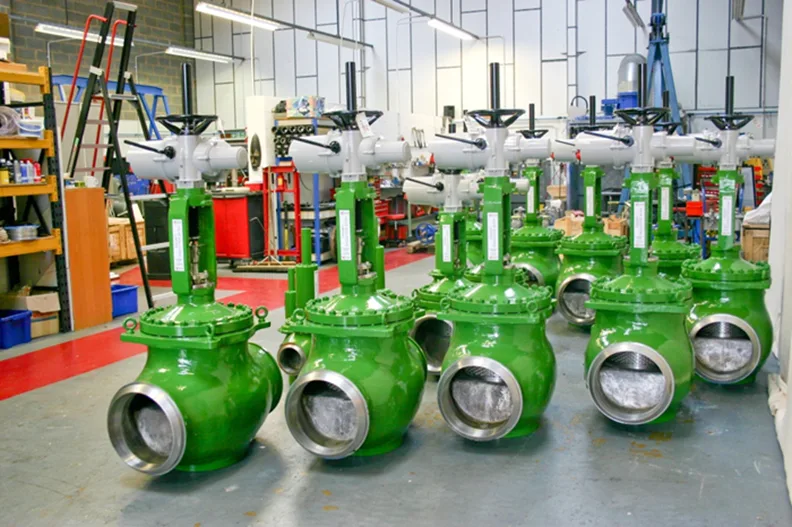